Understanding Silicone Membrane for Vacuum Press: A Comprehensive Guide
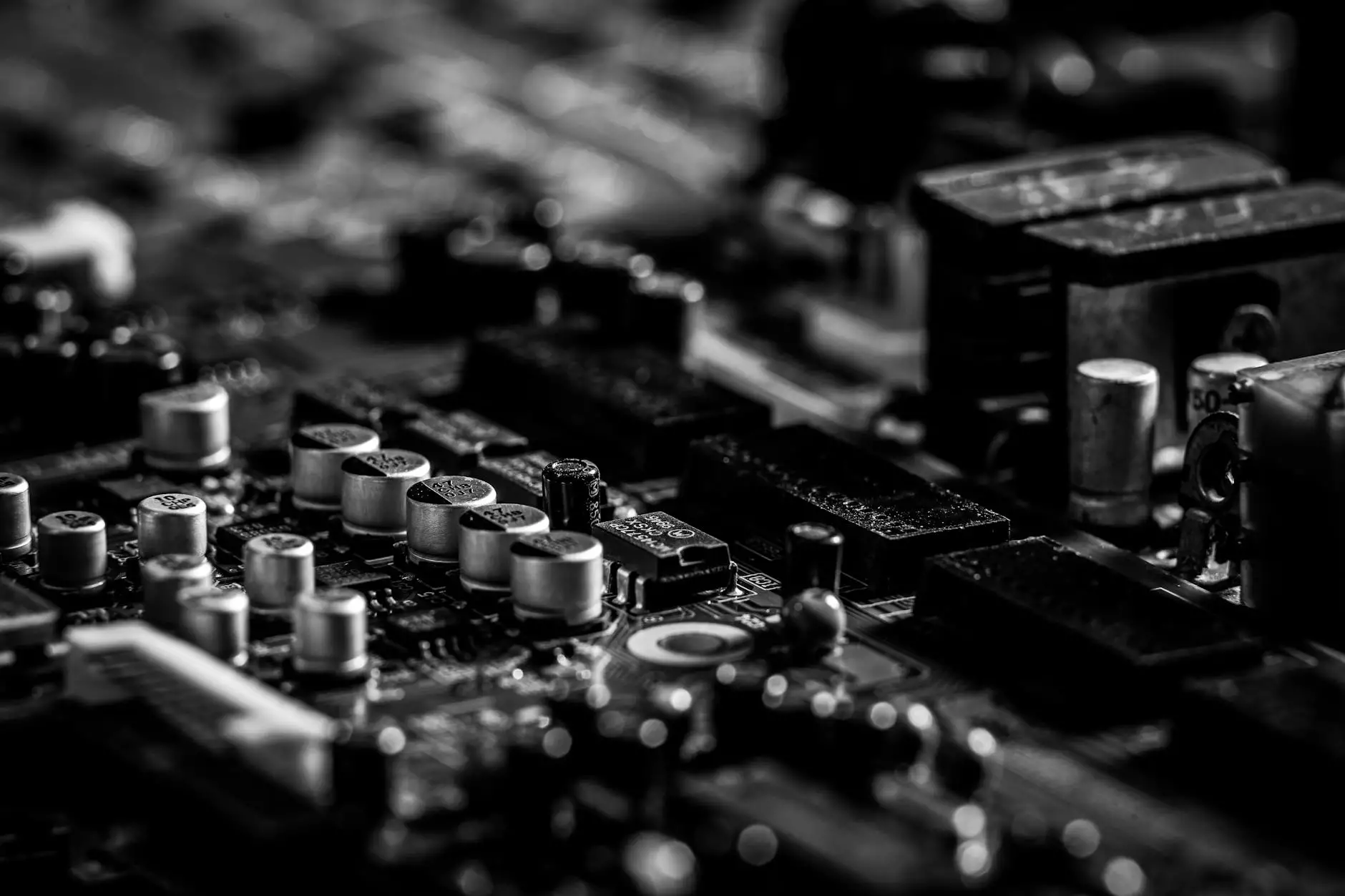
Introduction to Silicone Membranes
In the realm of vacuum presses, the use of silicone membranes has emerged as an essential component that significantly enhances efficiency and effectiveness. This article delves deep into what silicone membranes are, their characteristics, and their pivotal role in various applications.
What is a Silicone Membrane?
A silicone membrane is a thin layer of silicone rubber that is used in vacuum pressing applications. Its unique properties make it particularly well-suited for creating a vacuum-tight seal, which is crucial for the successful operation of vacuum presses.
Key Characteristics of Silicone Membranes
Silicone membranes boast several remarkable characteristics:
- High Durability: Silicone is known for its resistance to wear and tear, ensuring longevity and reliability.
- Temperature Resistance: They can withstand extreme temperatures, making them suitable for various industrial processes.
- Flexibility: The flexibility of silicone allows it to conform to different shapes, which is vital for effective vacuum sealing.
- Chemical Resistance: Silicone membranes are resistant to many chemicals, ensuring stability and reliability in diverse environments.
- Non-Toxic: Silicone is a safe and non-toxic material, making it suitable for applications in the food and medical industries.
Applications of Silicone Membranes in Vacuum Presses
The versatility of silicone membranes allows them to be utilized across multiple industries:
1. Woodworking Industry
In woodworking, silicone membranes for vacuum press systems are essential for laminating and veneering processes. They help achieve even pressure distribution, which results in a flawless finish.
2. Composite Manufacturing
Silicone membranes play a critical role in composite manufacturing. They allow for the efficient molding of materials like fiberglass and carbon fiber, providing a smooth surface and reducing the risk of air pockets.
3. Automotive Sector
Many automotive manufacturers rely on vacuum presses equipped with silicone membranes for processes such as paint application and part assembly. The membranes ensure a tight seal that enhances the quality of the finished product.
4. Food Industry
In the food sector, silicone membranes can be used for packaging applications. Their non-toxic nature and resistance to high temperatures make them highly effective for products requiring vacuum sealing.
5. Medical Devices
In the production of medical devices, the use of silicone membranes guarantees high precision and cleanliness, which are critical for compliance with industry standards.
Benefits of Using Silicone Membranes
Utilizing silicone membranes for vacuum presses offers numerous benefits:
- Enhanced Product Quality: By providing a consistent vacuum seal, silicone membranes improve the quality of the finished products.
- Increased Efficiency: The durability and flexibility of silicone membranes streamline the pressing process, leading to increased productivity.
- Cost-Effectiveness: The long lifespan of silicone membranes reduces the frequency of replacements, saving costs in the long run.
- Simplicity of Use: Silicone membranes are easy to install and operate, making them user-friendly.
Maintenance of Silicone Membranes in Vacuum Presses
To ensure the longevity of silicone membranes, it’s crucial to implement regular maintenance practices:
1. Cleaning
Regular cleaning is essential to remove any residues that can interfere with performance. Use a mild detergent and soft cloth to clean the membranes without damaging them.
2. Inspection
Periodic inspection for any signs of wear or damage will help identify issues before they escalate. Look out for cracks, tears, or changes in color.
3. Proper Storage
When not in use, store silicone membranes flat in a cool, dry place to avoid deformation. Avoid exposing them to direct sunlight for prolonged periods.
Choosing the Right Silicone Membrane
Selecting the appropriate silicone membrane for your vacuum press application is vital. Here are key considerations:
- Thickness: Choose a thickness that balances flexibility and durability.
- Size: Ensure that the membrane fits your vacuum press perfectly to avoid leaks.
- Temperature Rating: Consider the temperature range your application requires.
- Cost: While cheaper membranes are available, investing in higher quality silicone can yield better long-term outcomes.
Future Trends in Silicone Membrane Technology
As industries evolve, so does the technology surrounding silicone membranes. Here are some anticipated trends:
- Enhanced Material Properties: Research is ongoing to develop silicone membranes with improved properties, such as higher thermal resistance and better chemical compatibility.
- Customization: The demand for tailor-made silicone membranes that meet specific industry needs is growing.
- Sustainability: There is a shift towards environmentally friendly materials in the production of silicone membranes, aligning with global sustainability initiatives.
Conclusion
In conclusion, the role of silicone membranes for vacuum presses cannot be overstated. They are integral to enhancing the performance of vacuum pressing applications across various industries. From woodworking to automotive manufacturing and beyond, silicone membranes provide a reliable and efficient solution that improves overall product quality and efficiency. With ongoing advancements in material technology, the future looks bright for silicone membranes, promising even more innovative uses and enhancements. Investing in quality silicone membranes is not just a choice; it is a commitment to excellence in production.
silicone membrane for vacuum press